Water bottling (Filling) plant
Process and solutions
A water bottling plant performs a complex process that requires a high standard of professionalism. When we speak about water bottling, in fact, many topics rise as far as hygiene, safety, and pollution are concerned: to grant the successful completion of the process, you have to choose only the best machines available on the market.
You must understand these before purchasing as water filling machine.
- What kind of bottle are you going to use PET or Glass, what the mouth size (28 and 32 are common) ?
- Estimated Production capacity
- Is your water carbonated or not?
- Boxed or film wrapped cartons ?
- Self-adhesive or sleeve type label?
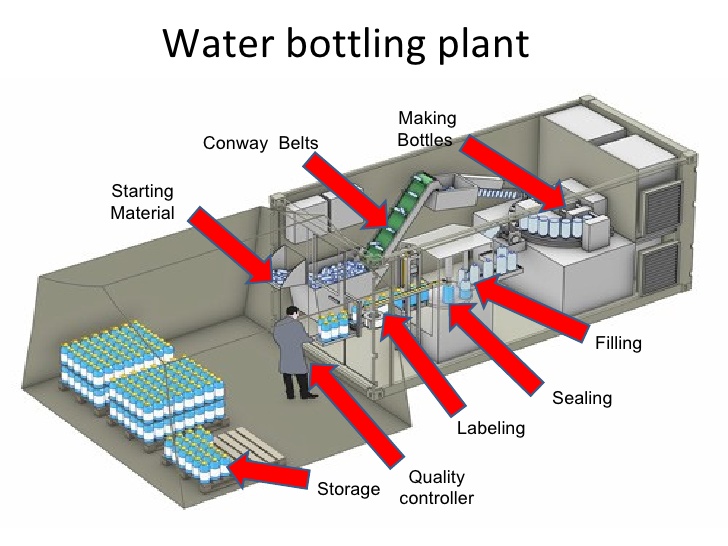
The process carried out by a water bottling plant includes five or six steps, depending on your decision to produce carbonated water or not:
- Cleaning: cleaning of the empty bottles is probably the most important step in a water bottling plant. The reason is simple: a proper cleaning is the only way to grant hygiene and safety to the water you are bottling. It would be a great mistake to sterilize water before the bottling, and then contaminate it just in the final process of the production. Therefore, choose only the best providers as far as cleaning machines are concerned: quality machines are made only with the best materials, resistant to rust and corrosion, and can be sanitized whenever you need.
- Filling: filling the bottles with water is obviously the aim of any water bottling plant. This process is quite simple: the bottles are grabbed by some grippers, while the nozzles over them pour the water into them. If you choose to bottle your water into glass only, you would better focus on a machine specifically designed for glass bottles; on the other hand, the same suggestion can be made if you fill the water in PET bottles only. In case you choose, instead, to produce both glass and PET water bottles, you can rely on a machine that supports both of them.
- Saturating: this process is included in a water bottling plant only if you have to produce carbonated water. You will have to provide, then, a saturation unit that could dearate the water and carbonate it with a device that directly injects the CO2 into the liquid.
- Capping: capping is the final step performed by a water bottling plant. The bottles are moved up to a capping machine that provides each of them with a cap and seal the water into protected atmosphere. After the capping, your water is ready to be put on the market and sold locally or on a higher scale.
- Labelling: Labelling is process of putting a label on the bottle, there are two common label, the sleeve type, which which like the name suggest it is a sleeve pressed from top down, and a sticker label, which can be a sticker (self-adhesive or with in-line glue to attach the label)
- Wrapping or Boxing: This is how your product goes to the market, as box or film wrapped? Film wrapped is most common, however, for high end water bottling boxes are more preferred, For film wrap can be fully automated in-line process with a rotary table and a tunnel heat shrink machine.
For big scale production look for USA (Spectrapac) or Italy (Comac) machine suppliers on our featured supplier list, for anything below 5000BPH Chinese or India machine are good and cheap enough